The HDPE geomembrane installation process is the most critical process in the entire anti-seepage system. The success or failure of the entire project depends on the construction quality of the artificial anti-seepage layer. Therefore, every process and every link during construction must be strictly organized and constructed carefully.
HDPE geomembrane construction technical requirements
Before laying the HDPE geomembrane, the geomembrane installation unit must provide the laying and welding layout of the anti-seepage membrane. It is required to choose the laying direction reasonably, reduce the stress on the joints as much as possible, and rationally arrange the position of each piece of material to minimize the joints. There shall be no transverse joints on the slope with a slope of 10% and within 1.5m of the slope foot.
Before laying the HDPE geomembrane, the owner and the supervising engineer should jointly conduct a comprehensive confirmation of the site conditions to ensure that the foundation surface of the landfill is smooth, without unevenness, sharp particles, and various types of particles that may damage the HDPE anti-seepage membrane. If there are hard debris, there should be no harmful debris within 25mm of the surface depth.
The quality of the geomembranes(various performance indicators, whether there are bubbles, holes, wrinkles on the surface, etc.) should be strictly inspected. Laying can be carried out after confirmation.
The HDPE geomembrane should be laid smoothly and firmly, with as few wrinkles as possible. After laying, it should be ballasted and anchored in time. The HDPE geomembrane should be laid with the smooth side up and the rough side down if applied on the slopes.
During the construction process, the influence of climate factors should be fully considered and allowances should be made for thermal expansion. The length of cold shrinkage.
Each piece of anti-seepage membrane must be welded on the day it is laid, and appropriate protection measures must be taken to prevent rainwater from entering the ground surface below.
Welding requirements for HDPE geomembrane:
(1)The welding form generally adopts double weld seam lap welding, and extrusion welding is only used in repairs (repairs, coverings) and places where double weld seam equipment cannot reach;
(2) The construction site should have sufficient welding construction equipment to ensure continuous welding construction;
(3) A testing laboratory should be set up at the construction site and equipped with necessary testing equipment, and on-site testing should include visual inspection, pressure test, vacuum test and destructive test of the anti-seepage membrane welding;
(4) Official welding shall not begin until the sample welded by the welding equipment has passed the trial welding inspection or been confirmed by the supervision engineer;
(5) If the ambient temperature is lower than 5°C or higher than 40°C, the construction unit should provide written proof of the same welding quality as within the specified temperature range, and ask the supervision engineer for confirmation before construction;
(6) Before welding, dust, dirt and other foreign matter on the surface of the anti-seepage membrane must be cleaned up, and the welding edges must be cleaned;
(7) When welding, try to keep the welding machine gun head perpendicular to the welding plane and maintain a certain pressure;
(8) When welding, you should always pay attention to the change of overlap width, and make corresponding treatment according to the actual situation. For double-rail fusion welding, the overlap width of the weld is not less than 100mm, and for extrusion welding, the overlap width is not less than 100mm. 75mm, the welding connection strength should not be less than the strength of the base metal;
(9) Extrusion welding must first use hot air to bond the upper and lower films, and use a grinder to remove the oxide layer on the film surface at the welding position in advance. The grinding width should be consistent with the width of the extrusion welding;
(10) After the anti-seepage membrane is welded, the weld seam should be sampled and the strength of the weld seam should be tested at the frequency of sampling every 150m of the weld length for each welding machine;
(11) For double-rail welding, the closed space formed by the anti-seepage membrane between the two welds should be subjected to air pressure leakage testing, and for extrusion welding, vacuum testing or spark testing should be used;
(12) Set the conductive layer downward.
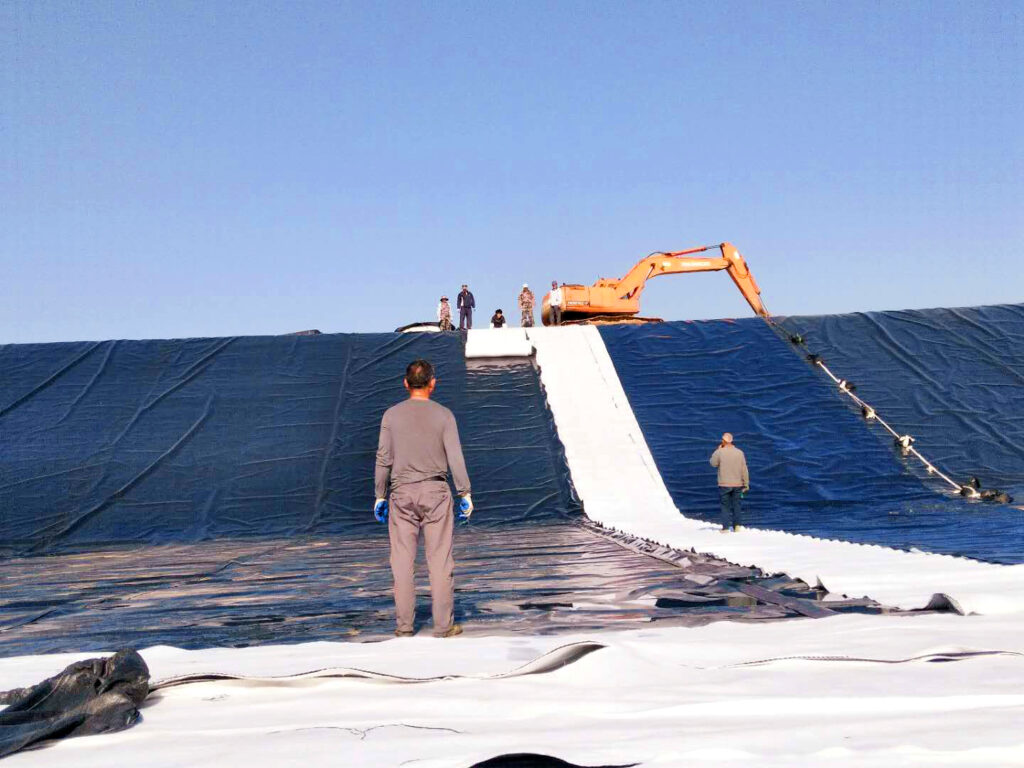
HDPE geomembrane anchorage requirements
(1) During the excavation of the anchor trench, the soil at the bottom of the trench must not be disturbed. The bottom of the trench is flat without loose soil, and the slope of the trench wall meets the design requirements; (2) Before the anchor trench is backfilled with soil, the bottom of the trench must not be soaked in water, and the accumulated water should be drained out in time; (3) The anchor trench should be backfilled in time, and the soil quality of the backfill should meet the design requirements. The backfill soil should be compacted in layers using a small tamping machine, and the compaction degree should not be less than 95%; (4) During the laying process, prevent any damage to geotechnical materials due to loading and unloading activities, high temperature, chemical leakage or other factors; (5) Laying tools must not cause damage to the normal function of the anti-seepage material, and the mechanical equipment used for construction must not cause obvious scratches to the anti-seepage material and damage to the laying base surface; (6) When adjusting the overlap width of materials during the laying process, the connected parts must not be damaged. When adjusting the position of the anti-seepage membrane after laying, the installed anti-seepage membrane must not be damaged; (7) During construction, sufficient temporary ballast (sandbags) must be provided to prevent the laid anti-seepage membrane from being blown up by strong winds. In the case of strong winds, the anti-seepage membrane must be temporarily anchored and the installation work must be suspended.

HDPE geomembrane construction administrative requirements
(1) Before laying and installing the HDPE membrane, invite the owner, designer, on-site supervisor and relevant units to conduct a pre-construction preparatory meeting. The meeting will ultimately determine the construction details of the anti-seepage construction and solve various new situations that arise on the construction site.
(2) Make sure all preparations including power line maintenance and unblocking before construction, maintenance of construction machinery and equipment in place, and labor arrangements are in place before construction.
(3) The membrane can be laid only after the lower layer of the membrane has passed the acceptance inspection. The HDPE membrane cannot be laid without acceptance.
(4) Construction must be carried out in accordance with the approved documents and after obtaining the project supervisor’s written consent to our construction proposal. Records should be kept during construction and filed with the owner for future reference.
(5) Construction equipment, machinery and HDPE geomembrane materials should be inspected before construction
(6) The HDPE geomembrane material certificate should be kept for future reference, the package should be opened to check the appearance quality of the HDPE geomembrane, and any discovered mechanical damage, production wounds, holes, breaks and other defects should be recorded and repaired.
(7) HDPE geomembranes that are damaged and difficult to repair should be cut off. The HDPE geomembrane material must be approved by the supervising engineer before construction.
Recent Posts
Author
Founded in 2002, Tinhy's team focuses on the manufacturing, marketing, installation, application and research and development of geosynthetic materials.
View all posts