HDPE geomembrane welding requirements
The HDPE geomembrane process is the most critical process in the entire anti-seepage system. The success or failure of the entire project depends on the construction quality of the artificial geomembrane. Therefore, in the construction, every process and every link must be strictly organized and carefully constructed.
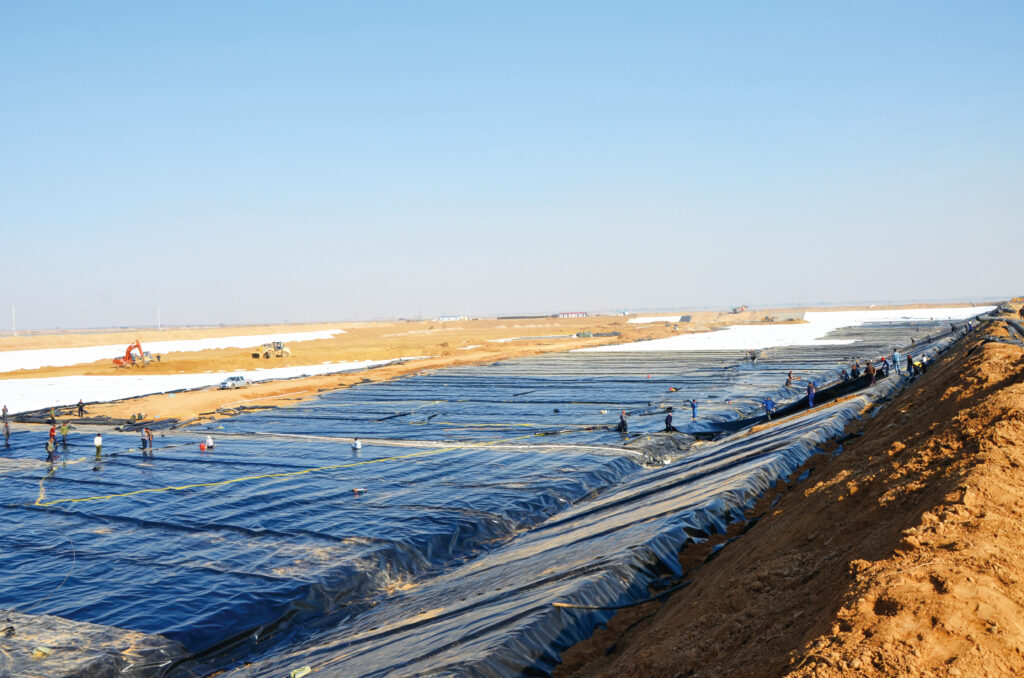
HDPE geomembrane welding generally adopts double seam lap welding, and extrusion welding is only used for repair (repair, covering) and places where double seam equipment cannot reach;
The construction site should have sufficient welding construction equipment to ensure continuous welding construction
The HDPE geomembrane construction site should have a testing laboratory equipped with necessary testing equipment, and the on-site testing should include visual inspection, pressure test, vacuum test and destructive test of the anti-seepage membrane welding
Formal welding of HDPE geomembrane shall not be started until the samples welded by the welding equipment have not passed the test welding inspection or the supervision engineer confirms
If the ambient temperature is lower than 5°C or higher than 40°C, the construction unit shall provide.
Written certification of the same welding quality within the enclosure, and the construction can only be carried out after confirmation by the supervision engineer;
Before HDPE geomembrane welding, the dust, dirt and other foreign matter on the surface of the anti-seepage membrane must be cleaned, and the welding edge must be cleaned
When welding, try to keep the torch head of the welding machine perpendicular to the welding plane and maintain a certain pressure
Pay attention to the change of lap width at all times during welding, and make corresponding treatment according to the actual situation. For the construction organization, design double-track fusion welding.
The lap width of the weld is not less than 100mm. For the lap of extrusion weld The width is not less than 75mm, and the welding connection strength should not be less than the base metal strength
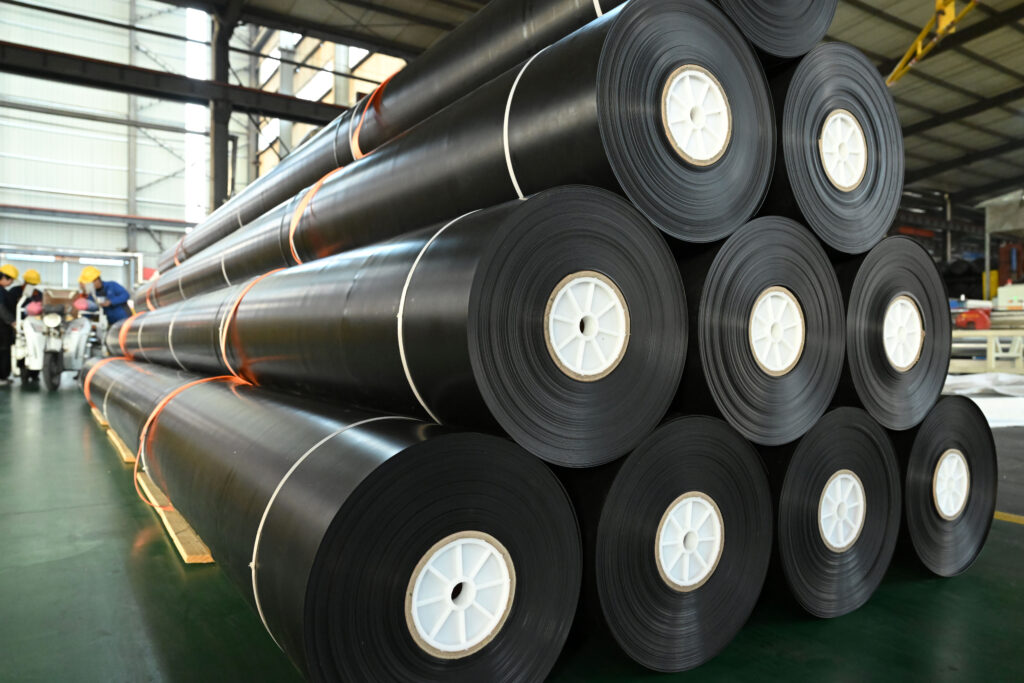
Extrusion welding must first use hot air to bond the upper and lower HDPE geomembranes together, and use a grinder to remove the oxide layer on the membrane surface at the welding position in advance, and the grinding width should be consistent with the width of extrusion welding
After the anti-seepage membrane is welded, the weld seam should be sampled and the weld seam strength should be tested according to the frequency of sampling the weld seam length once every 150m for each welder
For double-track welding, the closed space formed by the HDPE geomembrane between the two welds should be tested for air pressure leak detection, and vacuum testing or electric spark testing should be used for extrusion welding
The conductive layer of HDPE geomembrane is set downward.
As is known to all, geomembranes can be applied in many industries, such as waste landfills anti-seepage, water management, reservoirs anti-seepage projects, etc.
In recent years, with the development of geomembranes material science and the improvement of geomembranes performance, the application of geomembranes has become more extensive and the scale of their use has become larger and larger.
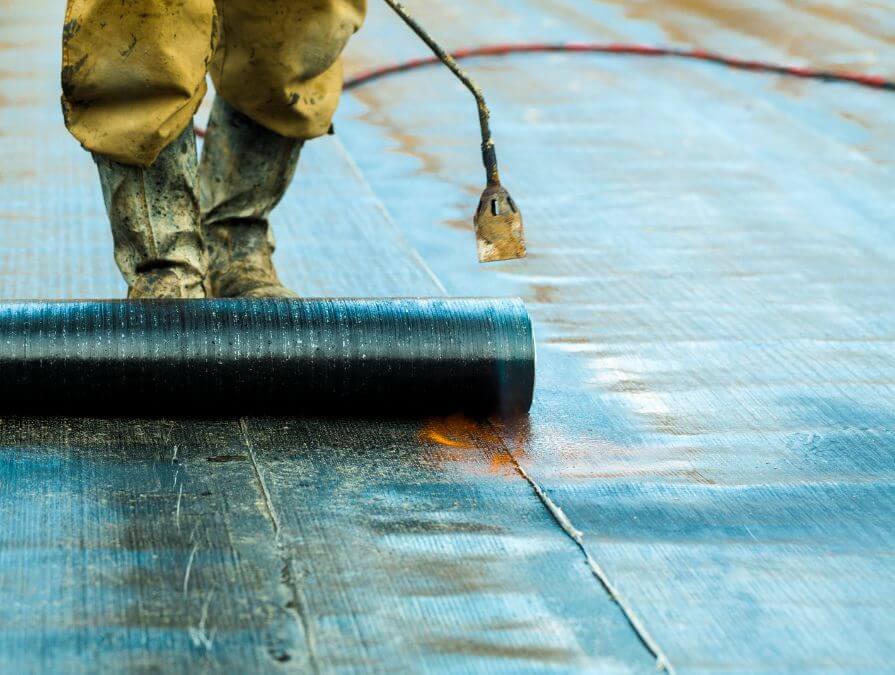
Geomembranes are gradually popular with engineering personnel due to their advantages of easier construction, shorter construction period, and lower cost.
The geomembrane used in landfill liner systems is typically 60 mil (0.06 inches) thick and consists of low permeability materials like high-density polyethylene (HDPE).
HDPE Geomembrane Liners can be applied in a variety of containment applications and the geomembrane barriers applied in landfills anti-seepage projects as the final cover system is typically 40 mils thick and consists of low-density linear polyethylene (LLDPE) with a thickness of up to 60 mils.
Author
Founded in 2002, Tinhy's team focuses on the manufacturing, marketing, installation, application and research and development of geosynthetic materials.
View all posts